Extract: A growing number of industries are relying on the superior disinfection and environmentally-friendly properties of Chlorine dioxide. Chlorine dioxide is quickly becoming the preferred bleaching agent in the pulp and paper industry because it minimizes the environmental impact of the bleaching process.
ClO2 is also used to not only disinfect municipal and drinking water supplies, but also control the water’s taste, odor and color.
In the food industry, chlorine dioxide disinfects water used to sanitize equipment and preparation surfaces, wash fruits and vegetables, and prevent salmonella and e-coli from contaminating meat and poultry.
In commercial and institutional applications, ClO2 is used to prevent the spread of legionella in hotels, hospitals and universities. Industrially, chlorine dioxide is an effective membrane treatment, as well as a biocide for cooling and wastewater. It is used in the production of ethanol, microelectronics, nitrogen and ammonia…
PureLine has a patented process to generate ClO2 on site using common salts, water, and electricity.
This is another great paper by
Dr. Greg Simpson.
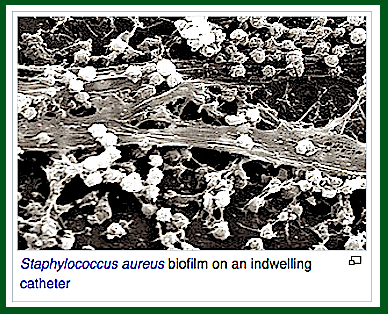
Biofilms create huge problems for companies. Operating industrial cooling systems with biofilms is costly and inefficient. Dr. Simpson discusses improving industrial cooling systems with Chlorine dioxide. Biofilms destruction is key to operations and the reason why Chlorine dioxide is the preferred biocide. Please contact PureLine for a full re-print of this paper (complete with references). PureLine is your ClO2 GO2!
Abstract:
Chlorine dioxide has several performance characteristics that make it ideally suited for microbiological control of industrial cooling systems, particularly those which are highly contaminated with organics or ammonia.
One of its performance characteristics is
the ability to disperse/dissolve/remove biofilm.
This paper discusses the use of chlorine dioxide for control of bacteria and the associated biofilm in industrial cooling systems. The methods of application and expected results are described. The relatively slow bacterial recovery that is observed in systems treated with this oxidant is discussed. In addition a number of case histories are presented which illustrate the effectiveness of this versatile oxidizer.
Introduction:
Bacterial biofilm cause numerous problems in industrial plants including restrictions in heat transfer, corrosion by direct bacterial action, and corrosion by action of bacterial enzymes3 which may occur even after cell death. Because biofilm tends to be patchy and non-uniform over the surface, the differences in the oxygen concentration at the metal surface result in corrosion. In addition, the anaerobic conditions created under a healthy biofilm promote the growth and development of the highly corrosive sulfate- reducing bacteria, SRB, Desulfovibrio desulfuricans.
Indirectly biofilm causes other problems. A biofilm provides a tacky surface where microscopic particulates of marginally soluble mineral scale, corrosion products, or silt can accumulate. Under high heat transfer rates, as the biofilm denatures, the deposit becomes more inorganic in nature because water constitutes a large portion of the biofilm. It is not uncommon for this type of problem to be erroneously ascribed to a ‘scaling’ or deposition problem. Once the thickness of the biofilm exceeds that of the viscous sublayer, significant reductions in water flow can occur. Flow reductions, far greater than can be explained by a simple reduction in effective pipe diameter, have been observed in some systems.
Gaseous chlorine has been used historically to control bacteria and their associated biofilm. Chlorine, while acceptable as a disinfectant at neutral pH’s, becomes less effective with increasing pH. In addition, chlorine has been shown to be ineffective at controlling biofilm in some cases10. The pressures that have been brought to bear on use of gaseous chlorine have encouraged the evaluation of various alternatives. One common replacement has been various forms of bromine. Those who have used bromine have observed that for clean systems, performance is acceptable. For systems contaminated with organics, however, neither performance nor costs of bromine-based biocides are acceptable.
One alternative that has been shown to have the best performance characteristics in terms of both disinfection and control/removal of biofilm, is chlorine dioxide.
Properties of Chlorine Dioxide:
Chlorine dioxide is a gas at ambient temperatures and pressures. Due to its tendency to decompose in the vapor state at concentrations exceeding about 10% in the presence of impurities, it is never stored, shipped or used in the gaseous form. Instead, it is produced as a dilute aqueous solution. A more in-depth discussion of the decomposition of chlorine dioxide as it relates to industrial applications is given elsewhere.
Generation of Chlorine Dioxide:
For applications requiring less than a few tons per day of chlorine dioxide, the most common chemistry of generation of chlorine dioxide is by the oxidation of sodium chlorite. Generally, a solution of sodium chlorite is mixed with a solution of chlorine. Gaseous molecular chlorine will react with the chlorite very rapidly to produce dilute aqueous solution of chlorine dioxide (Equation 1). The chlorine can also be in the form of hypochlorous acid, i.e., from the addition of bleach and acid prior to its reaction with the chlorite (Equation 2). This reaction is somewhat slower but is still rapid enough so that good reaction efficiencies are attained.
Equation 1 2NaClO2 + Cl2 > 2ClO2 + 2NaCl
Equation 2 2NaClO2 + NaOCl + HCl > 2ClO2 + NaOH + 2NaCl
For an in-depth discussion of generation technologies, the reader is referred to the review by Gates.
Characteristics of Chlorine Dioxide:
Chlorine dioxide occupies a unique position among the various oxidizers used in industrial plants.
It is a weaker oxidizer than other commonly used oxidants, i.e., it has a lower oxidation-reduction potential as shown in Figure 1.
At the same time it has greater oxidation capacity, that is, unlike the other commonly used oxidants, it has the capacity to accept up to 5 electrons in an oxidation-reduction reaction (Figure 1).
It is generally less reactive with the various materials likely to be encountered in cooling systems than other commonly used oxidants. As a result of its greater selectivity, its oxidizing power, its oxidation capacity and its affinity for reduced sulfur compounds, chlorine dioxide can be viewed as a ‘niche’ oxidizer. For some applications, nothing can come close in terms of performance.
Treatment of Cooling Systems:
The method of treatment of cooling systems depends on the desired goal. For example, if the plant heat exchangers and other water-cooled equipment are the target, chlorine dioxide will be fed to the suction side of the recirculating pumps, to get circulation throughout plant equipment.
If one particular exchanger is troublesome, then it is possible to treat at a specific exchanger. McGuire and Dishinger observed that the reaction of chlorine dioxide with biofilm was so rapid that one critical biofouled exchanger could be cleaned before the entire cooling system bulk water was disinfected.
If the cooling tower fill is the problem, as is commonly the case with high efficiency plastic type fill, then either the return header or specific headers can be treated, allowing treatment of individual cells. Treatment typically is 1—2 mg/L based on recirculation rate. It is based on recirculation rate because chlorine dioxide is considered a once-through treatment chemical, because it is commonly thought that chlorine dioxide is lost over a tower, it being volatilized and stripped from solution. For slat fill towers this is generally true, although a small amount does recycle. However, for plastic film fill type towers it is not true as less chlorine dioxide is lost to atmosphere with the high efficiency plastic fill than with the splash fill. The reason is that aside from the initial spraying that the water sees above the fill, minimal other splashing occurs. It is in part this fact that allows cleanup of high efficiency plastic fill with chlorine dioxide. Several case histories follow which illustrate the ability of chlorine dioxide to remove and control biofilm.
Case History 1:
A southwest electric arc furnace steel mini mill had a 1 million-gallon reservoir from which cooling water was taken. A small cooling tower was located at one end and the recirculation pumps were located at the other end of this large basin. Because this reservoir was open to sunlight a healthy population of algae was established. The algae provided a significant demand for biocide and oxidant. The algae also made conditions favorable for growth of more common aerobic bacteria.
The cooling water cools many things in such a plant. One critical area is that of the ‘molds’. Molds are a copper, water-cooled, specially designed form through which molten steel is allowed to flow. The purpose of the mold is to cool the molten steel sufficiently to allow a thin ‘skin’ to form on the outside of the molten steel. The molten steel can then be worked to any desired shape in the mill. Any hot spots which forms on the water-side of the mold can result in a ‘break-out’, i.e., the skin does not form in one spot and the molten steel flows from the desired shape. When a breakout occurs, the line must be stopped, and the mold taken from service. The steel which has poured out of the line must be cleaned up and reworked. The number of times a mold can be reused, i.e., the number of ‘heats’, before it must be reworked is referred to as mold life. Problems had been so bad in the past that only 8—12 heats per mold on one strand could be achieved.
Historically, this mill had used bleach, bleach with bromide, bromine tablets, chlorine tablets, and a number of non-oxidizing biocides. Nothing had performed acceptably. Chlorine dioxide was fed to pump suction at 1—2 mg/L. Within a few hours, the light green color of the basin began to change. Samples were taken and filtered through a .45 micron filter. The filters, which had been light green at the start of the trial, turned to a light tan color. Within a few days, substantial improvement in heat transfer became apparent. Complaints about air conditioning in the plant that had been rife, disappeared. Over the next several months, plant personnel began to slowly increase the number of heats. At one point the number of heats reached 500, yet plant personnel decided that it was best to limit heats to mold manufacturers guidelines. Today, the plant runs in the 300—350 heats per mold range. This trend is shown pictorially in Figure 2.
Plant savings from costs to rework or replace molds and rework the steel from breakouts was estimated to be somewhere between $100,000—$400,000 annually, the lower number reflecting reworking of existing molds and the higher number reflecting mold replacement. Plant records did not include this information. In addition, the cost of chlorine dioxide was around 60% of the cost of the various alternatives used previously.
Case History 2:
The cooling system in this southwestern natural gas liquids plant had a microbial fouling problem. Plant operations had lived with this problem so long that it did not appear to be a problem. Chlorine tablets and two non-oxidizing biocides were added routinely, and although bacterial tests of the bulk water showed bacterial levels to be low, exchanger backwashing was required routinely. It is instructive to note that bulk water bacterial testing provides indications of system cleanliness only when chlorinating continuously and a ‘free chlorine’ residual is maintained. There is evidence that planktonic bacterial are quite different from sessile bacteria in terms of their physiology, nutrient requirements, and resistance to bacterial disinfection.
The high frequency of necessary exchanger backwashing also required a significant amount of makeup water. The makeup water was of such poor quality that partial sodium zeolite softening was required. Backwash water and zeolite regeneration water flowed to two large evaporation ponds which were essentially full. Chlorine dioxide was fed to pump suction at 1—2 mg/L. Within several days, plant throughput increased by 15% and has remained at this level due to improved heat transfer. Plant management estimates that increased production has added around $500,000 to bottom line profits. Since implementation of this program, one of the two evaporation ponds has been taken out of service, due to virtual elimination of required backwashing. Level in the other pond has also decreased dramatically.
Case History 3:
In one southwestern gas plant, microbiologically fouled high-efficiency PVC honeycomb fill was limiting the heat rejection capacity of the cooling tower. Production was curtailed and plans were in place to shut the tower down a cell at a time and manually remove and clean the fill. Microbiological control in this plant was accomplished strictly by use of non-oxidizing biocides. Demand in the water for chlorine dioxide was significant, as makeup well water had a substantial level of light hydrocarbon present. In addition, all of the plant wastewater was used in a waterflood. Water flow through the continuous monitors required by the waste water system was wasted to the cooling tower. The high contamination of sulfide, organics and bacteria present in this water (prior to treatment for waterflood use) also created a significant demand for oxidant. Chlorine dioxide was fed at 5 mg/L to the riser of one cell for 48 hours, although demand was so great that only 0.2—0.3 mg/L of chlorine dioxide was measured in a water sample taken just above the fill. A section of the fill is shown before and after treatment in Figure 3. The success of this treatment has led to a number of applications specifically to clean up and to prevent microbial fouling of such fill.
Case History 4:
A small cooling system in one southwestern refinery serviced 15 exchangers. Each exchanger had a backup to provide duty during the mechanical cleaning required 3—4 times per year. Intimate contact of process hydrocarbon and entrained gases with cooling water occurred as a direct result of the two atmospheric condensers used in this unit. The high level of organic and sulfide in the water resulted in severe biofouling. Fouling was so severe that throughput was limited. In addition, corrosion rates were in excess of 10 mpy on carbon steel.
Each exchanger was backwashed weekly, or more frequently as determined by process outlet temperature. Once fouling became so severe that backwashing had little effect, the exchanger was mechanically cleaned. The exchanger which was nearest its required mechanical cleaning was taken from service, opened, and photographed to establish a benchmark, and returned to service.
Chlorine dioxide was fed to the recirculating water pump suction at a few mg/L. Feed rates were kept at this level to prevent any massive sloughing of biofilm mats and potential plugging of exchangers, particularly the lube oil coolers and other small coolers which had no backup and very small diameter tubes. So much hydrocarbon existed in this system that 5 days passed before any residual was found in the pump discharge. It is interesting to note that chlorine dioxide was fed into the pump suction and residuals were measured on the pump discharge. This illustrates the extremely rapid kinetics of reaction of chlorine dioxide, it being consumed by material in the bulk water within seconds. Within 36 hours after the residual had been found in the pump discharge, i.e., demand in the bulk water had been met, the temperature of the process out of the exchanger that was nearest its required mechanical cleaning had gone from a maximum of 107 °F to a minimum of 53 °F (ambient temperatures were in the 30’s). No process changes had occurred. The only parameter which changed was the cleanliness of the exchanger. This exchanger was again inspected after the cleanup phase of the trial. A comparison of this exchanger before and after system cleanup is shown in
Figure 4.
Discussion:
Chlorine dioxide, although it has a greater oxidation capacity, usually accepts only one electron in an oxidation-reduction reaction. This raises the question as to why chlorine dioxide is so effective at disinfection and biofilm removal. For disinfection, some have suggested that as a gas it can permeate bacterial cell walls much easier 23. Its affinity for reduced sulfur compounds, including the sulfhydryl group, has also been suggested as one mode of bacterial disinfection 24. Whatever the mode of action, it appears that chlorine dioxide disrupts some vital cell process, causing rapid cell death. For biofilm removal, other factors appear to be involved. For an open recirculating cooling system in a petroleum refinery, petrochemical plant or gas plant, the recirculation rate is in the range of 10—15% of the system volume. This means that the entire volume of the cooling system will be displaced 4—6 times in an hour. If a material were to be fed to the system on the basis of recirculation rate at 1 mg/L, the concentration of this material would be 4—6 mg/L after one hour, neglecting blowdown or other losses. For chlorine dioxide, 50—70% of the chlorine dioxide converts to chlorite in the disinfection, oxidation, biofilm removal process. Thus, at the end of the intermittent treatment, around 2—4 mg/L of chlorite ion would remain in the system for a significant period of time. This chlorite, a relatively poor disinfectant and oxidant, will remain in the system and be lost only through blowdown. The presence of chlorite creates other interesting possibilities regarding biofilm control and bacterial recovery.
The Role of Chlorite on Disinfection and Biofilm:
During numerous field trials bacterial recovery or rebound was slower than expected. This had been attributed to a complete removal of bacterial biofilm, making it more difficult for the bacterial population to re-establish. Subsequent inspections revealed that while much of the biofilm had been removed, some biofilm was still intact. Questions remained about the slow bacterial recovery.
Several observations have led to the conclusion that chlorite has a significant effect on bacterial recovery and biofilm growth. Masschelein noted that while chlorite is not very effective as a disinfectant, it has bacteriostatic properties, and retards the rate of bacterial rebound in potable water systems. In this way, the chlorite slows the regrowth of biofilm. Clark and Langley demonstrated biofilm removal by adding ‘stabilized chlorine dioxide’ to a system and then adding a bacterial nutrient. This nutrient resulted in an increase in bacterial activity that in turn resulted in a higher acid production in the biofilm. As the stabilized chlorine dioxide moves through the biofilm, chlorine dioxide is released by the action of acid on the chlorite. Biofilm removal resulted.
In one potable water system, chlorine dioxide was consumed in the distribution system, the residual disappearing. Yet the residual reappeared at the end of the distribution system26. Reasons were not known, although one recent explanation was that traces of residual chlorine reacted with the chlorite to produce a measurable residual of chlorine dioxide. Based on the above observations, it may have been the result of biofilm action that regenerated the chlorine dioxide.
Summary:
Chlorine dioxide’s unique performance characteristics make it unmatched for many applications.
It has been used in cooling systems, although widespread use has not occurred. Unless chlorine did not perform adequately, conditions prevented its use, or economics were not good, historically there was no reason to consider chlorine dioxide.
In most of these cases, use costs for chlorine dioxide was less than chlorine.
For some systems use costs of chlorine dioxide have been somewhat greater than chlorine. In such systems, i.e., systems generally considered to be ‘clean,’ cost savings resulting from improvements in heat transfer have greatly outweighed any incremental increases in the cost of the chlorine dioxide program. Improvements in heat transfer in many cases have been extraordinary.
With increasing environmental pressures to eliminate gaseous chlorine, with the increasing emphasis on water reuse issues, and the safety concerns of storing and handling chlorine cylinders, momentum is building to find alternatives. When alternatives to gaseous chlorine for microbiological control in cooling systems are considered, chlorine dioxide should certainly be included. On a performance basis, chlorine dioxide remains unmatched, especially when improvements in heat transfer are included.
.
Reproduced by:
.
We have reproduced this document
here because the original online
one was difficult to read, and
the photos had gone?
.